Hemp Plastic: A Sustainable Solution for a Greener Future
- kyleoliveira
- May 24, 2023
- 6 min read
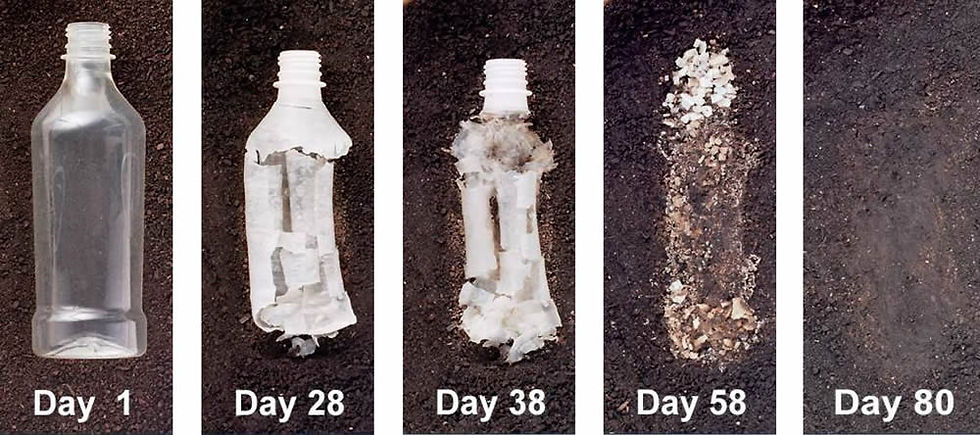
In recent years, the world has witnessed a growing interest in sustainable alternatives to traditional materials. One such innovation gaining significant attention is hemp plastic. With its remarkable properties and eco-friendly nature, hemp plastic is emerging as a promising solution for a greener future. In this article, we will explore the various aspects of hemp plastic, including its properties, manufacturing process, applications, environmental impact, and future outlook.
I. Introduction
Definition of Hemp Plastic
Hemp plastic, also known as hemp bioplastic, is a type of biodegradable plastic made from hemp fibers. Unlike conventional plastics derived from fossil fuels, hemp plastic is sourced from the fibers of the hemp plant, making it a renewable and sustainable alternative.
Growing Interest in Sustainable Alternatives
With the increasing awareness of environmental issues and the need for sustainable practices, industries and consumers alike are actively seeking greener alternatives. Hemp plastic has gained traction due to its potential to reduce the environmental impact associated with traditional plastics.
Benefits of Hemp Plastic
Hemp plastic offers several advantages over conventional plastics. Firstly, it is biodegradable, meaning it can break down naturally without leaving harmful residues behind. Additionally, hemp plastic exhibits remarkable strength and durability, making it suitable for various applications. Furthermore, it is a versatile material that can be molded into different shapes and sizes. Lastly, hemp plastic is cost-effective compared to some other sustainable alternatives, making it an attractive choice for businesses.
II. Properties of Hemp Plastic
Hemp plastic possesses a unique set of properties that make it an excellent alternative to conventional plastics.
Biodegradability
One of the key advantages of hemp plastic is its biodegradability. Traditional plastics can take hundreds of years to decompose, contributing to pollution and landfill overcrowding. In contrast, hemp plastic can naturally degrade within a few months to a few years, depending on the specific composition and environmental conditions. This property significantly reduces the long-term environmental impact associated with plastic waste.
Strength and Durability
Hemp plastic exhibits impressive strength and durability, making it suitable for various applications. The fibers extracted from hemp plants are known for their tensile strength, which translates into robust and long-lasting plastic products. Whether used in automotive parts, packaging materials, or consumer goods, hemp plastic can withstand rigorous use without compromising its integrity.
Versatility
Hemp plastic is a highly versatile material that can be molded and shaped to meet specific product requirements. Its flexibility allows for the creation of intricate designs and customized solutions. From small consumer items to large structural components, hemp plastic offers designers and manufacturers the freedom to explore innovative possibilities.
Cost-Effectiveness
Compared to some other sustainable alternatives, hemp plastic offers a cost-effective solution. With the increasing demand for eco-friendly materials, economies of scale are being realized in the production of hemp plastic, leading to reduced costs. This affordability makes it a viable choice for businesses seeking sustainable options without compromising their bottom line.
III. Manufacturing Process of Hemp Plastic
The manufacturing process of hemp plastic involves several steps, from the extraction of hemp fibers to the final product.
Extraction of Hemp Fibers
The first step in the production of hemp plastic is the extraction of fibers from the hemp plant. The hemp stalks are harvested and processed to separate the long, strong fibers from the woody core. This process typically involves mechanical separation techniques to ensure high-quality fibers.
Processing and Blending
Once the hemp fibers are extracted, they are processed to remove impurities and achieve the desired consistency. The fibers are then blended with a biopolymer, such as polylactic acid (PLA) or polyhydroxyalkanoates (PHA). This blending process ensures a strong bond between the hemp fibers and the biopolymer matrix, resulting in a durable and stable material.
Molding and Shaping
After the blending process, the hemp plastic mixture is ready for molding and shaping. Various techniques, such as injection molding or extrusion, are used to form the desired shapes and structures. The molded hemp plastic products can be further processed, painted, or finished to meet specific requirements.
IV. Applications of Hemp Plastic
Hemp plastic finds applications in diverse industries due to its unique properties and eco-friendly nature.
Automotive Industry
The automotive industry has recognized the potential of hemp plastic in reducing the environmental impact of vehicle manufacturing. Components such as interior panels, dashboards, door panels, and trims can be made from hemp plastic, offering weight reduction, increased fuel efficiency, and improved sustainability.
Packaging Industry
In the packaging industry, hemp plastic is gaining popularity as a sustainable alternative to traditional plastic packaging. From bottles and containers to bags and films, hemp plastic packaging provides an eco-friendly solution that is both functional and environmentally conscious.
Consumer Products
Hemp plastic is also making its way into a wide range of consumer products. Items such as phone cases, kitchenware, toys, and personal care products can be manufactured using hemp plastic, offering consumers sustainable choices without compromising on quality or functionality. Even companies such as Lego have considered using hemp as an alternative to fossil-fuel derived plastic.
V. Environmental Impact of Hemp Plastic
Hemp plastic contributes to a greener and more sustainable future by addressing several environmental concerns associated with traditional plastics.
Reduction of Carbon Footprint
The production of hemp plastic generates a significantly lower carbon footprint compared to conventional plastics. Hemp plants naturally absorb carbon dioxide during their growth, acting as a carbon sink. This carbon sequestration, combined with the use of renewable resources in hemp plastic production, results in a reduced overall greenhouse gas emissions.
Decreased Reliance on Fossil Fuels
One of the major advantages of hemp plastic is its ability to reduce reliance on fossil fuels. Traditional plastics are derived from non-renewable resources such as crude oil. In contrast, hemp plastic utilizes the fibers from the hemp plant, which can be grown and harvested sustainably, without depleting finite resources.
Less Waste Generation
The biodegradable nature of hemp plastic contributes to a significant reduction in waste generation. When hemp plastic products reach the end of their lifecycle, they can decompose naturally, returning to the environment without leaving behind harmful microplastics. This characteristic helps alleviate the burden on landfills and prevents plastic pollution in ecosystems.
VI. Challenges and Future Outlook
While hemp plastic shows great promise, there are several challenges that need to be addressed for its widespread adoption.
Legal and Regulatory Barriers
The legal and regulatory landscape surrounding hemp cultivation and hemp-derived products can vary significantly across regions. Harmonizing regulations and providing clear guidelines will facilitate the growth of the hemp plastic industry.
Scaling Up Production
As the demand for hemp plastic increases, scaling up production capabilities becomes crucial. Investing in infrastructure, research, and development will be necessary to meet the growing market needs and ensure a stable supply of hemp fibers.
Potential for Innovation and Growth
Despite the challenges, the future of hemp plastic looks promising. Ongoing research and development efforts aim to improve the material's properties, manufacturing processes, and expand its range of applications. Continued innovation will unlock new opportunities and contribute to a more sustainable future.
VII. Conclusion
Hemp plastic offers a sustainable and eco-friendly alternative to traditional plastics. Its biodegradability, strength, versatility, and cost-effectiveness make it a compelling choice for industries and consumers seeking greener solutions. The manufacturing process of hemp plastic, coupled with its diverse applications, demonstrates its potential to revolutionize multiple sectors. By reducing carbon footprint, decreasing reliance on fossil fuels, and minimizing waste generation, hemp plastic plays a vital role in building a greener future. Embracing hemp plastic and supporting its growth is a significant step towards creating a more sustainable and environmentally conscious society.
FAQs (Frequently Asked Questions)
Is hemp plastic as durable as traditional plastic?
Yes, hemp plastic exhibits impressive strength and durability, making it suitable for various applications. It can withstand rigorous use without compromising its integrity.
2. How long does hemp plastic take to biodegrade?
The biodegradation time of hemp plastic can vary depending on the specific composition and environmental conditions. Generally, it can degrade within a few months to a few years, significantly shorter than the hundreds of years traditional plastics take.
3. Is hemp plastic more expensive than traditional plastic?
Yes, however, compared to some other sustainable alternatives hemp plastic offers a cost-effective solution . As the demand for eco-friendly materials grows, economies of scale are being realized, leading to reduced costs.
4. Can hemp plastic be recycled?
Yes, hemp plastic can be recycled. However, it is important to separate it from traditional plastics during the recycling process to ensure proper treatment and maximize its environmental benefits.
5. Are there any regulations regarding the production and use of hemp plastic?
The regulations surrounding hemp cultivation and hemp-derived products can vary across regions. It is important to comply with local laws and regulations when producing and utilizing hemp plastic.
Comments